
Healthcare facilities
Healthcare facilities should provide a free from diseases service, yet when not properly treated provide the source of many infectious nosocomial pathogens, including methicillin-resistant S. aureus (MRSA), Clostridium difficile, norovirus, Acinetobacter, and vancomycin-resistant Enterococcus (VRE). Environmental surface cleaning programs should be carefully developed because microorganisms attached to environmental surface are more resistant to sanitizing agents than free-living counterparts.
MicroKill have proven to be highly effective, up to 99.99+% in total number of microorganisms removed from healthcare facilities within a significantly shorter contact time and no signs of resistance and regrowth.
MicroKill can be used to treat eye infections like blepharitis and pinkeye, medical reports show that it is also effective in curing a wide range of bacterial and virus eye infections. The salt concentration in MicroKill is very similar to tears guaranteeing no adverse health reactions if its sprayed or splashed into your eyes.
Food industry
Pathogenic and spoilage organisms may be present in and on foods, but only a few of these are a serious health concern because of their ability to cause human illness. The most frequent or serious causes of food borne bacterial infections include viruses, notably noroviruses and hepatitis A, parasites such as Cryptosporidium and Cyclospora, molds such as Aspergillus spp., and bacteria such as Salmonella Enterica., E. coli O157:H7, Clostridium botulinum, and Listeria monocytogenes.
Food safety is ensured largely, but not exclusively, by controlling the presence and growth of pathogenic organisms in and on foods. Numerous cleaning compounds and processes have been developed to remove and destroy bacteria, viruses, and parasites from equipment and surfaces in food processing plants and from fresh produce and animal carcasses. It is a significant challenge to maintain a clean environment in food processing plants. Antimicrobial compounds are used to eliminate or limit the growth of pathogens in foods, but these are typically costly toxic chemicals.
MicroKill is revolutionizing cleaning, sanitization and disinfection solutions for the food industry by providing a safe and ‘Green’ solution to help protect the nation’s food supply.
Independent studies have discovered the following benefits of MicroKill when used in food processing:
-
Absolute and effective control of target bacteria
-
Direct contact or clean in place (CIP) applications
-
Toxic-free environment for employees, risk mitigation
-
Cost effective
-
Safer supply chain for consumers
MicroKill is non-toxic, inexpensive to produce, and can be used in multiple applications due to its various inherent sanitizing characteristics. Food retailers can use it to wash incoming products, sanitize equipment, prevent cross-contamination and keep their facilities clean. It can be used in food storage facilities in fogging systems to kill airborne pathogens or for the manufacturing of packaging ice used for example in the fish industry. Food processors can use it for cleansing processing equipment, eliminating biofilm from piping systems, and disinfecting surfaces and facilities. Food preparation facilities can use MicroKill to sanitize equipment and food prep areas to reduce the possibility of causing or spreading food borne illness.
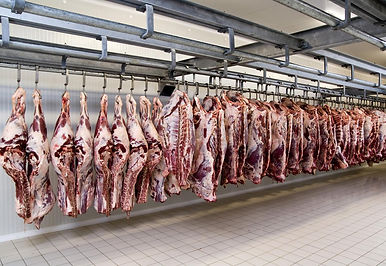



Brew and Beverage
In the multibillion-dollar beverage industry, it is crucial that manufacturers produce consistent quality. Limited returns allow for sustained enhancement of brand image and equity. Food and beverage processing rely on water as its main ingredient and water quality needs to be of the highest possible standard. Under typical conditions, process or ingredient water is filtered repeatedly before use. While this procedure is effective, other sources of microbial contamination do exist. If left unchecked, these will likely result in product contamination and spoilage.
Numerous applications for MicroKill have been identified and used in the cleaning and sanitizing of beverage facilities:
-
Cleansing and disinfecting of bottles
-
Disinfecting of main water source used for production
-
Cleansing and disinfecting of tubes, containers and tanks
-
Removal of biofilm in tubes and disinfecting pipes after use
The results have shown:
-
An increase in production time and overall operating efficiency due to shorter CIP's and down time
-
Water usage may be reduced by up to 60%
-
MicroKill will not affect the taste, color and appearance of the treated products
Agriculture
In spite of the significant leaps achieved in the field of food safety, various foodborne diseases, food-related outbreaks, and different types of product losses during the food supply chain still occur and many plant and animal pathogens continue to pose serious concerns for the agricultural community. Acute food-borne disease infections and intoxications are much more of a concern to governments and the food industry today than a few decades ago.
Based on the above an efficient disinfection and cleaning program is required to ensure that microbial safety is achieved and guaranteed. Such a disinfection program can be applied both as a pre-harvest step in seed treatment, product yield improvement, product quality improvement, pathogen suppression, and plant disease control as well as a post-harvest intervention aiming not only to eliminate pathogenic bacteria but also to control product loss, for the shelf-life extension, against undesirable fungi, for chemical removals such as pesticide inactivation and toxin inactivation or mitigation procedures.
MicroKill has been proven to be an effective antifungal agent against various types of diseases in the field of agriculture. These diseases have been dealt with up to now with the application of fungicides during the crop season or prior to harvest. This practice imposes growers with a significant amount of added cost. In addition, fungicides have other disadvantages such as negative environmental impacts and occupational exposure danger during fungicide applications on the field. Moreover, there is a growing demand by consumers for limiting the application of chemicals such as fungicides in the agricultural production of all crops. Hence, alternative methods with similar or even better efficiency and fewer negative effects are necessary and MicroKill has proven to be one of these new types of antifungal treatments.
A typical application of MicroKill in this field is the spray of agricultural products with the solution through an overhead irrigation system. This technique has provided excellent results in the microbial control of various plants and fruit such as strawberry, cucumbers, tomato, etc.

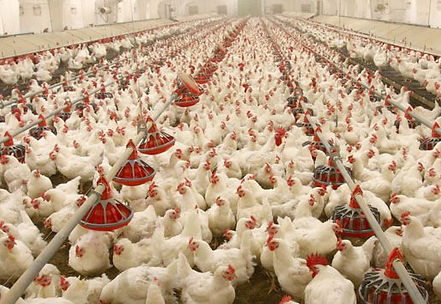



Water Treatment
Amongst the measures taken to ensure a constant supply of potable water, has been the development of rehabilitation techniques of boreholes or water wells. This is a practical method of restoring the original capacity (yield) without having to drill additional wells at high cost.
MicroKill for the treatment of Water Wells is extremely effective in improving well performance by removing biofilm and softening hardened plugging layers within the screen and gravel pack due to a kill efficiency superior to that of most chemicals traditionally used.
Bio-Fouling
MicroKill rehabilitates wells that are classified: Dried-up
When water yields from boreholes declines, the source is deemed to have "dried up". The catalyst for most holes "drying up" is in reality biological fouling (bio-film). It is estimated that approximately 80% of the issues pertaining to water wells were caused by biological fouling. Nearly 50% of boreholes worldwide lose yield as a result of bio-fouling. It chokes both the aquifer as well as the ground surrounding the borehole through which the water to the borehole flows, including the screens (casing and pump) within the borehole. Supply diminishes and the hole achieves a status of ‘non-viability’.
MIC (Microbial Induced Corrosion) bio-film is another chief cause effecting piping, screens, membranes, filters and pumps. It is estimated that MIC can shorten the operational life of a pump by more than half.
MicroKill kills the most virulent waterborne pathogens and bacterium present in wells and water supplies prevalent in developing countries such as Tuberculosis, Clostridium difficile, Staphylococcus aureus, Pseudomonas aeruginosa, Norovirus, Legionella and many other known pathogens.
MicroKill has been proven effective in the treatment of both potable and wastewater systems. Its biocidal capabilities can be applied anywhere water is used or processed by dosing it directly into the system, without causing a strong chlorine taste or smell. Treated water can also eliminate or reduce pathogens from surfaces it contacts. Similarly, equipment (ice machines, dental unit water systems, beverage dispensers, endoscopes, countertops, etc.) in contact with treated water will be cleared or reduced of pathogens and be kept free of mineralization and biofilm.