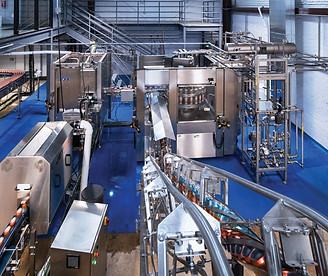
Manufacturing

In any manufacturing setup, it is crucial that manufacturers produce consistent quality. Limited returns allow for sustained enhancement of brand image and equity. Food and beverage processing rely on water as its main ingredient and water quality needs to be of the highest possible standard. Under typical conditions, process or ingredient water is filtered repeatedly before use. While this procedure is effective, other sources of microbial contamination do exist. If left unchecked, these will likely result in product contamination and spoilage.
Uses of MicroKill in manufacturing
Numerous applications for MicroKill have been identified and used in disinfecting and sanitizing of manufacturing facilities:
-
Treatment of source water
-
Disinfectant supply to clean-in-place (CIP) and sterilise-in-place (SIP) systems
-
Rinsing of bottles, necks and closures
-
Replacement of steam sterilisation
-
Allowing reduced water temperatures in hot washes
-
Permanent disinfection during a running filling process
-
Mist and fog spray to treat contaminated air
-
System wash downs

Benefits of using MicroKill in Manufacturing

The results have shown:
-
A reduction in chemical use: Typically we replace chlorine dioxide and peracetic acid with MicroKill. This has significant cost and health and safety benefits
-
Less handling of hazardous chemicals and less hazard generation (there is no risk of toxic gasses or explosive atmospheres with the MicroKill)
-
An increase in production time and overall operating efficiency due to shorter washdown time and down time
-
MicroKill will not affect the taste, color and appearance of the treated products.